CASE STUDY
Traditional Pipe Coating Failure
HDD Pipeline Protection
Project Data
Location | Fayetteville, AR |
Completion | 2023 |
Project Type | HDD Full Encapsulation Testing |
Products Used | Denso Bore-Wrap® |
Contractor or Applied By | Denso & Raphoon, LLC |
Horizontal Directional Drilling (HDD) has been used to install pipelines since the early 1970s. Over nearly 50 years, the industry has learned a great deal about how to successfully install pipes beneath rugged terrain, bodies of water, buildings, homes, roads, etc. An entire industry has developed around HDD, which includes equipment, installation companies, publications, specialty tooling, engineering, consulting and more. Organizations such as the Pipeline Research Council International (PRCI) and American Petroleum Institute (API) have done significant testing and research around HDD installation methods and ways to achieve the best results. Documentation has been produced to include best practices in design, and guidance systems have been created that are so sophisticated the travel of the drill pipe can fall within less than 1% variation of the designed path. Even with all of this advancement, one of the largest pipeline operators in America can still experience this level of damage on their attempted HDD installations.
With incredible resources, tools, design specialists, and years of experience, there is a component of every single HDD that cannot be controlled. That is the ground content that exists along the pathway. While core samples can tell you what you may face, it is never the whole story. The pipe pictured was installed by a leading pipeline company following their design path and passing through their chosen soils while attempting to install the pipe beneath a road in Arkansas. After completing the drill hole, reaming it to the appropriate diameter and pulling the pipe in using their standard practices, the pipe arrived on the other side of the hole with incredible amounts of visible damage to the pipeline coating and some deformation of the steel. The company elected to pull the pipe back out and take another approach. They utilized a commonly applied ARO coating solution as their field joint coating protection. However, that coating had also failed in those areas. In an attempt to solve the problem, they reached out to one of the distributors of Denso products and were offered Denso Bore-Wrap as a solution. Bore-Wrap is a shear, abrasion, impact, and gouge (SAIG) resistant coating protection specifically designed to withstand the threats from HDD installation.
The Denso representative reviewed the conditions and recommended a product trial to evaluate the level of protection needed for the pipe and the anti-corrosion layer to survive the installation. The operator also wanted to reassess their historical option at the same time. The decision was made to pull in 2 joints of pipe. On the test pull, the leading section was wrapped in 4 layers of Bore-Wrap. Behind that, the operator applied their historical epoxy solution for coating protection, then on the trailing side, the minimum 2 layers of Bore-Wrap was applied.
Pulling the pipe into the same hole that caused the initial damage, we could see how much additional protection was necessary to have the anti-corrosion coating intact after installation. On the leading edge of the pipe, the 4 layers of Bore-Wrap shows almost no wear damage at all, with only a slight scratch visible along the side. Immediately following the layers of Bore-Wrap, the damage originally seen in this HDD became evident again. When the scratching got to the operator’s selected epoxy solution, “the way we always do it” as they said, the epoxy was removed entirely, leaving only a shadow of where it had been with several scratches into the plant-applied ARO. Finally, the scratches reached the minimum layers of Bore-Wrap. And again, the Bore-Wrap SAIG protection did its job. A small bit of Bore-Wrap took some damage at the leading edge before the sources of the gouging and impacts bumped up onto the body of the Bore-Wrap, and the damage was eliminated along the remainder of the length.
When the testing was complete, Bore-Wrap was able to protect the pipe from the hazards of this aggressive HDD hole. Where 50 years of experience, engineering, design, and best practices had failed (including the operator’s SOP for coating protection), Bore-Wrap was able to provide the missing component necessary for a successful installation. Over the past 3 years, this sentiment has been repeating over and over and while several pipeline operators have switched to SAIG resistant coatings, many, if not most continue to do what they have always done. But with the upcoming changes from DOT and PHMSA with the implementation of the “Mega Rule,” it is highly likely that we will see some very expensive consequences for those who continue to use the same old ARO coatings they’ve always used.
Bore-Wrap offers a fast, field-applied, durable and easy solution to a significant issue faced in the HDD market. This company could have saved several hundred thousand dollars in rework by adding 2 layers of Bore-Wrap to the pipe before the installation took place.
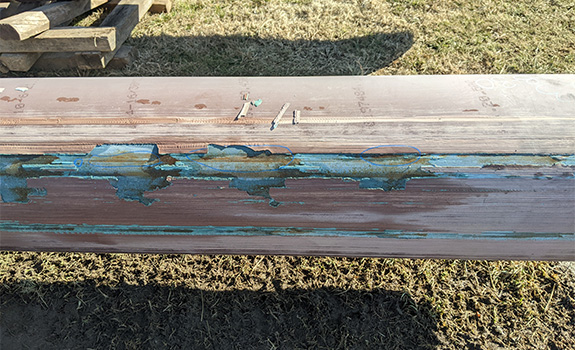
Traditional ARO coating failure on HDD install.
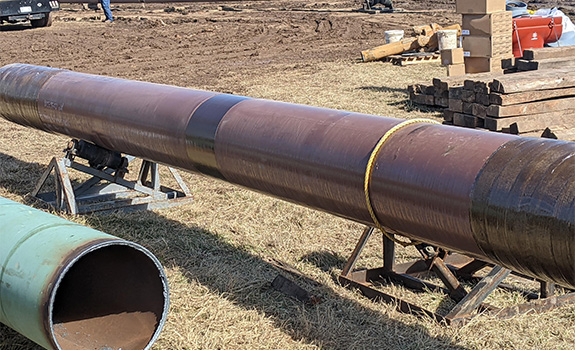
Test pull pipe with 3 options for protection.
Pull-head after installation with 4 layers of Bore-Wrap.
Test pull damage without a SAIG protection.
Competitor ARO completely missing.
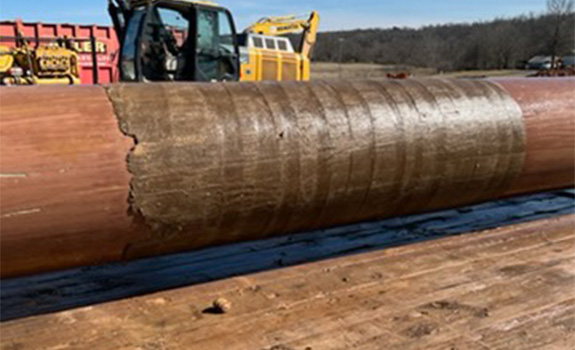
Bore-Wrap in 2 layers protects the anti-corrosion from damage.
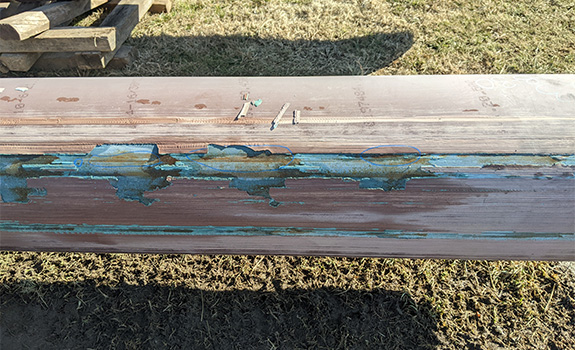
Traditional ARO coating failure on HDD install.
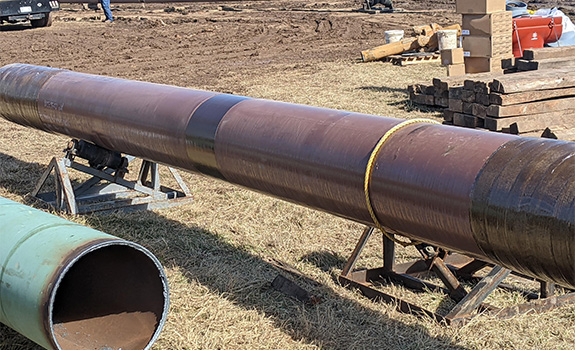
Test pull pipe with 3 options for protection.
Pull-head after installation with 4 layers of Bore-Wrap.
Test pull damage without a SAIG protection.
Competitor ARO completely missing.
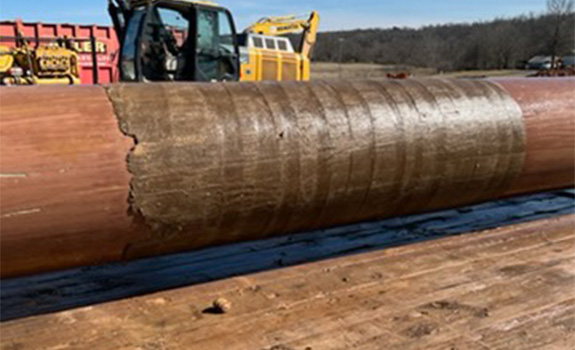